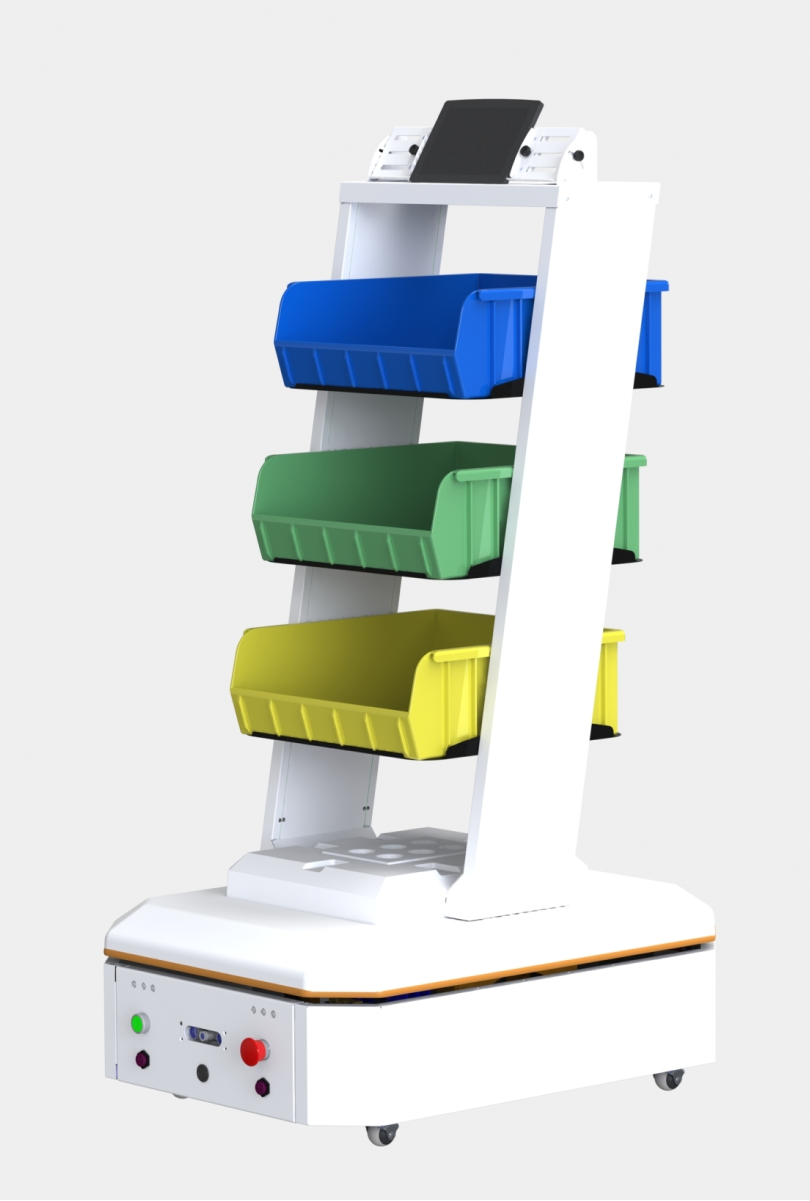
retail fulfillment amr
- 3x IMPROVES WORKER PRODUCTIVITY
- 3X ENABLING HIGHER PICK RATES
- 30% LOWER LABOR COSTS
- SIMPLE USER INTERFACE
According to a recent research report by ABI Research, it is predicted that by 2025, more than 4 million commercial robots will be installed in 50,000 warehouses. This includes a range of industries, from ecommerce and manufacturing to hotels and restaurants. As orders continue to put stress on warehouse operators, businesses are investing in both extra labor and automation to increase efficiency.
Fortunately, there is a solution that can help businesses reduce trips by 30-80% and double productivity using simple Autonomous Mobile Robot (AMR) or Automated Guided Vehicle (AGV) solutions. These solutions can minimize no value-added walks and maximize productivity, providing critical labor productivity gains in an environment of fierce competition and rising costs.
In a tough labor market, where businesses are struggling to hire and retain workers while balancing costs and benefits, AMRs and AGVs can be a cost-effective solution that doesn't require ongoing employment costs. Unlike human workers, these robots can be easily scaled up or down as needed.
For example, let's consider the simple use case of using autonomous mobile robots to automate the process of moving goods within a warehouse. By implementing AMRs or AGVs, businesses can easily increase enterprise productivity, save time and resources, and gather data for further optimization and scaling.
In fact, studies have shown that these solutions can reduce travel time by up to 80%, increase efficiency by up to 200%, and reduce operating costs by up to 50%. It's no wonder that businesses are turning to AMRs and AGVs to optimize their operations and stay competitive.
Don't let your business fall behind - contact us today to learn more about how AMRs and AGVs can benefit your organization.
Order a demo, and our team will analyze your enterprise within a 3 days, select processes for automation, and implement an autonomous robot in next 1 week! Results will appear within a three weeks!
* - Limited offer. Valid until July 30, 2023.
ELIMINATES WASTED WALKING TIME. Higher productivity, less aisle traffic
Robot-centric environments low human interaction
easily reconfigurable
Use case
Moving products from point A to point B, using the example of a manufacturing enterprise producing autonomous mobile robots (ironically, such enterprises also need automation).
Let's imagine that the enterprise has a sheet metal processing workshop, laser cutting, cleaning, bending and, possibly, a few more operations. Of course, this enterprise has carried out several iterations of optimising the location of the shops and the sequence of operations according to the Lean methodology. That is why the painting shop is only 30 m and almost in a straight line from this metal processing shop.
Thus, the next operation is painting and the parts will follow exactly there, suppose that the workshop is intensively loaded and earlier the worker transported the parts in portions of 100 kg by the trolley (cart) using his muscular efforts. At the same time, the average speed of such movement is approximately 1 m/s (3.6 km / h) and it takes about 30 seconds for a cart and a muscular worker (labourer) to overcome 30 m and about the same for the way back.
This used to be the case, however, after the employee pulled his back yet again and the production line began to lose productivity, the wise owner decided to do a simple experiment. The owner suggested to the employees (they worked in two shifts of 8 hours with a break for lunch) that they no longer do this traumatic, difficult, not value added work, but they are going to learning courses to learn how to do specific professional work. And for the transportation of goods, the simplest and inexpensive AMRs will be used.
Note that we are considering a case where you can use your AMR as easy as a vacuum cleaner out of the box, using a clear simple user interface without WMS integration, any development, on-site testing and deployment or training. Indeed, the latest trend in the market is the simplification of the implementation and operation of industrial robots, including the reduction in the cost of the robot, the transition to modular elements to simplify maintenance.
The picture below shows the user interface, which allows you to easily and intuitively set up the robot and start working on the simplest user case described above.
Why choose to switch to a robotic system instead of using manual labor?
The bottom line is this – a robotic system is usually able to run 95 percent more efficiently than the average laborer during any given shift. Humans require breaks, days off, and their bodies get tired throughout their shift. Robots do not run into this problem, and in many cases, a robot can perform the work of up to four manual laborers, per shift (that’s why robots are not reading this article now - just busy on work).
That shows the return on investment in the labor cost savings alone.
ROI = (Gain from Investment – Cost of Investment) / Cost of Investment)
Calculating the different factors involved in the Cost of Investment is where things get tricky. In addition to initial equipment prices and installation costs, operating costs, as well as the effects on cash flow and profitability must also be taken into consideration.
Summarising:
- We have two employees who, on average, have a moving speed with a load equal to 3.6 km/h or 1 m/s.
- We want to completely replace the operations of moving goods with autonomous robots, the average speed of which will be 2 m/s (7.2 km/h) - i.e. productivity increase by 2 times;
- To overcome the distance from the metal processing shop to the paint shop with a distance of 30 mm and two turns at the entrance and exit from the shop, a person spends 30 seconds, and a robot - 15 seconds;
- The AMR battery capacity is 56A/h that is 10-14 hours (two robots work in two shifts, the total activity time of both robots is more than 20 hours);
- To charge one robot, 1.5 kW of electricity is needed, at a cost of 0.315 euro cents, charging will cost 50 cents. Two robots = 1 euro.
- We accept that the workers work 350 days a year, then 350 euros will be needed for the charge.
- Based on our research, on our partners' manufacturers feedback, the cost per such AMR is approximately $15,000, plus 10 percent annual maintenance.
- We estimated average annual labor costs per worker of $33,600 (roughly $17.50/hour).
- We used these costs to estimate the time to achieve ROI close to 100% achieving 2X greater productivity with robots than without.
Human | VS | Robot | |
Number of Humans workers: 2 | Number of AMRs: 2 | ||
Active working (2 labourers, 2 shifts):
7 hours, 1 hour break X2=14 hours/day | Working hours: 14 hours on one charge (0.5 Euro per charge for each robot) | ||
Cost per hour: 17.5 Euro x2=35 Euro
| _____ | ||
Cost per year: 67200 Euro
(2 workers, excluding vacation, state holidays, etc) | Cost per year: 24315 Euro
(15000 Euro per robot x2 = 30000 Euro; Service & Maintenance, 10%=3000 Euro; Charging = 350 for both per year) |
ROI = 80% (1st year)
Annual investments are almost 3 times lower!
Twice as efficient!
Scalability as a bonus!
win-win LIMITED offer
Improving our product and keeping abreast of the needs of our End Customers - we offer automation of warehouses and manufacturing SMEs on uniquely favorable terms!
- Navigation accuracy - 0.1m;
- Speed, maximum - 2 m/s;
- Maximum distance to detect obstacles - 40 m;
- Battery capacity - DC 24V 48Ah (12 hours of active work);
- Carrying capacity, up to - 120 kg (up to 500kg);
- Web interface for robot control, settings and analytics (local, web).
Contact us
We are happy to discuss cooperation and answer your questions.